Specialist Overview to Casting Aluminum : Strategies, Tips & Tricks
Mastering the Art of Aluminum Spreading Solutions: Every Little Thing You Required to Know
In the realm of production and engineering, aluminum spreading solutions stand as a critical method with a wide variety of applications. From detailed auto parts to aerospace components, mastering the art of aluminum spreading requires a deep understanding of the process, materials, and techniques entailed. As we explore the subtleties of this craft, revealing the complexities of aluminum casting services exposes a world where expertise, advancement, and accuracy assemble to form the future of various sectors.
Recognizing Light Weight Aluminum Spreading Refine
When delving into the realm of aluminum spreading, a basic aspect to understanding is the complex process associated with changing liquified light weight aluminum into solid things. The process starts with the melting of aluminum in a heating system at temperature levels exceeding 1200 ° F, turning it right into a liquified state all set for casting. Once molten, the aluminum is poured into a pre-designed mold and mildew tooth cavity, which figures out the form and qualities of the last item. The molten aluminum is left to cool and solidify within the mold and mildew, a vital step that determines the high quality and accuracy of the spreading.
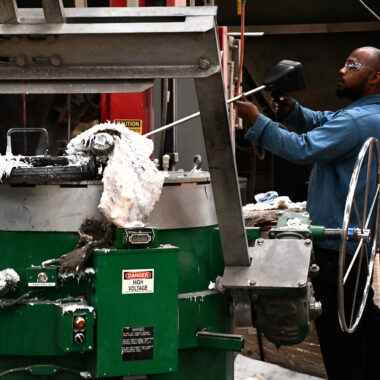
Advantages of Light Weight Aluminum Casting Provider
Having actually gotten an understanding of the elaborate aluminum spreading procedure, it is essential to now explore the considerable benefits used by light weight aluminum spreading solutions. Among the key advantages of light weight aluminum casting is its adaptability in producing complicated forms with high accuracy. This procedure enables elaborate layouts and thin walls that might be impossible or difficult to accomplish with other making methods. In addition, light weight aluminum spreading solutions are cost-efficient due to the relatively low price of resources and the efficiency of the casting procedure, leading to reduced labor costs.
Moreover, aluminum casting uses excellent deterioration resistance, making it excellent for a large range of applications in various markets, consisting of auto, aerospace, and electronics. The light-weight nature of light weight aluminum likewise adds to fuel effectiveness in transportation applications. Aluminum casting services provide high strength-to-weight proportions, ensuring sturdy and dependable end products. One more benefit is the recyclability of light weight aluminum, advertising sustainability and environmental responsibility in producing procedures. Overall, the advantages of aluminum spreading services make it a favored selection for many sectors seeking high-quality, affordable, and versatile manufacturing options.
Different Sorts Of Light Weight Aluminum Casting
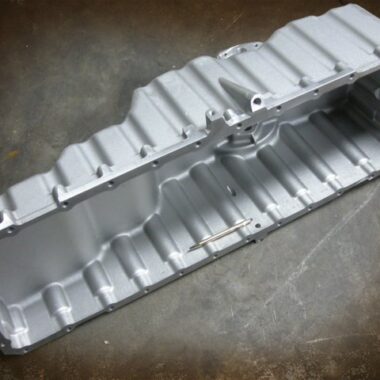
Pass away casting is an extremely effective procedure that involves injecting liquified steel into a steel mold and mildew under high stress. It is commonly used for mass production of small to medium-sized components with superb surface coating and dimensional precision. Sand spreading, on the various other hand, is an extra traditional technique where a pattern is used to develop a cavity in a sand mold and mildew, into which the molten steel is put.
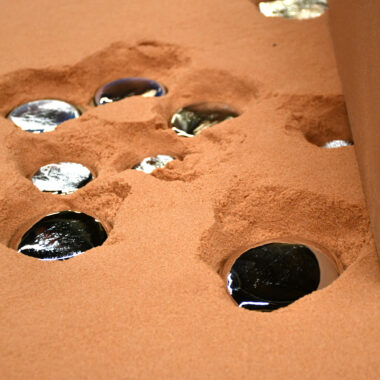
Variables to Think About in Light Weight Aluminum Spreading
Variables influencing the choice of light weight aluminum casting approach consist of manufacturing volume, part complexity, and expense factors to consider. Production volume plays an important duty in determining one of the most suitable spreading approach. For high-volume manufacturing runs, procedures like die casting or permanent mold spreading are typically liked as a result of their capability to quickly create large amounts her response of parts. On the various other hand, for reduced volume demands or prototypes, sand casting or financial investment casting may be better suited selections, as they provide better adaptability and lower tooling prices.
When picking a light weight aluminum casting technique,Part intricacy is one more critical element to think about. Detailed parts with complex geometries might call for an extra intricate casting official statement procedure, such as lost wax casting, to properly duplicate great details. Simpler parts, on the various other hand, can frequently be effectively created making use of easier casting approaches like sand spreading or die casting.
Expense considerations likewise play a substantial role in the decision-making procedure. While die spreading may use high-speed manufacturing capabilities, it typically requires expensive tooling, making it preferable for large production quantities where the tooling prices can be amortized over lots of parts. Sand spreading, on the other hand, may be a much more cost-effective choice for smaller manufacturing runs as a result of its lower tooling prices and versatility.
Tips for Improving Light Weight Aluminum Casting Skills
Developing skillful aluminum spreading abilities needs a detailed understanding of casting techniques, material residential properties, and top quality control actions. To improve your light weight aluminum casting skills, think about the adhering to pointers:
Master the Essentials: Before trying complex casting projects, guarantee you have a solid understanding of essential spreading strategies. Exercise fundamental puts, mold and mildew prep work, and gating systems to construct a strong foundation.
Understand Product Behavior: Light weight aluminum alloys exhibit one-of-a-kind buildings throughout the spreading process. Find out just how various alloys behave under varying temperature levels and pressures to optimize your casting end results.
Purchase Top Quality Equipment: High-grade devices and tools can significantly influence the success of your spreading jobs. casting aluminum. Buy accuracy instruments, crucibles, and molds to accomplish constant and trusted results
Continuous Learning: Remain upgraded on the most recent innovations in light weight aluminum casting technology and methods. Participate in workshops, workshops, and training programs to broaden your knowledge and skills.
Verdict
In final thought, grasping the art of aluminum casting services requires a thorough understanding of the process, factors, types, and advantages included. By honing your skills and taking note of details, you can improve the high quality and performance of your aluminum casting jobs. casting aluminum. With practice and commitment, you can come to be competent in aluminum casting and accomplish effective lead to your tasks
Having gotten an understanding of the elaborate light weight aluminum spreading procedure, it is critical to now check out the significant advantages provided by aluminum casting solutions. Furthermore, light weight aluminum spreading solutions are affordable due to the fairly low price of raw materials and the performance of the casting procedure, resulting in decreased labor costs.
Financial investment casting, additionally recognized as lost-wax spreading, is an accuracy spreading investigate this site method that can create detailed shapes with high precision. For high-volume manufacturing runs, procedures like die casting or permanent mold casting are usually favored due to their capability to rapidly create large amounts of components. Easier components, on the various other hand, can frequently be successfully generated using easier casting techniques like sand casting or die casting.